[ad_1]
It appears that Long Covid is not just affecting humans; increasing evidence suggests that the shutdowns during the pandemic have resulted in numerous mechanical issues for agricultural machinery across the nation.
Reliability challenges have surfaced in tractors, forage harvesters, telehandlers, and implements within the JD Townley & Son fleet based in Ballygowan, with a common factor being that all these machines were manufactured in 2020.
“Every piece of equipment we acquired that year has let us down,” says James Townley.
“I am convinced that the limited workforce on production lines during that time affected the assembly quality.”
See also: Contractor Comment: Infuriating weather sees new kit sit idle
About the Contractor
James Townley is a third-generation contractor at JD Townley & Son, providing a full range of agricultural services throughout County Down.
Business Overview
JD Townley & Son, Ballygowan, County Down
- Main Services: Grass and maize silage, cultivation and drilling, combining, square baling, spraying, slurry spreading
- Additional: 130ha farming, land drainage
- Team: James and Roy Townley, along with five full-time staff and an additional two or three during peak seasons
This season, the chief culprit has been James’s New Holland T7.270, which has accumulated an astonishing number of issues within just a few months of operation.
Among its problems are minor electrical issues—such as problems with the battery, starter motor, spool valve controller, and corroded wiring—along with a malfunctioning handbrake, a burst brake pipe, and a broken door handle.
While these issues were frustrating and relatively easy to fix, the complications surrounding the T7’s after-treatment system have posed a more significant challenge.
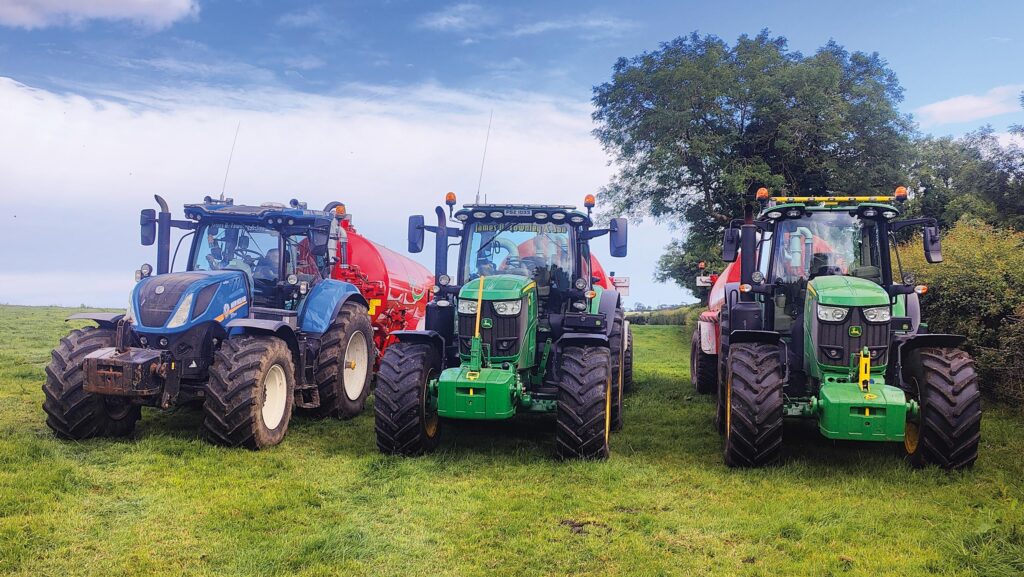
© James Townley
Error codes start appearing every 20 hours or so, forcing the tractor into “limp” mode, and no amount of regeneration efforts or an acid washout of the particulate filter has resolved the issue.
The T7 has been in the local dealership since mid-July, pending a complete exhaust assembly replacement.
Fortunately, New Holland is assisting with the costs, but with the drilling season approaching, time is critical.
“It seems like the dealer’s number has become a regular contact for us lately, but we’re fortunate with how quickly they’ve responded,” James notes.
“Nonetheless, this doesn’t deter us from considering another New Holland tractor for when we replace the T7.270.”
“We run a mixed fleet and each brand has had its share of issues—reliability is an overall concern.”
“The sheer number of sensors present today may not significantly enhance productivity, especially regarding emissions systems; if one sensor fails, it can cripple operations.”
The pandemic-related issues have also plagued the Jaguar 970 once again.
After already replacing a turbo and engine last year, this time, a persistent issue with the EGR pipe caused repeated breakdowns every few hours during the first-cut silage.
“It failed six or seven times, leading to complete power loss,” states James.
“Unfortunately for the mechanic, he always found himself fixing it while the engine was still hot—eventually, we replaced it with a thicker pipe that seems to have resolved the issue.”
New John Deeres Arrive
This past spring saw the addition of two John Deere tractors, which are both deemed downgrades from their predecessors.
Replacing a 7,000-hour 6195R with a 6R 175 and a 9,000-hour 6210R with a 6195M has resulted in significant cost savings.
“The M was £17,000 less than a comparable R, and for tasks such as trailer hauling and operating the Doda slurry pump, there isn’t much difference in performance. It essentially does everything an R can,” James explains.
“The smaller cab doesn’t concern me—though some of the crew might disagree— and the reduced horsepower boost appears to enhance engine torque.”
“It offers more grip and feels more agile than the Rs, which might be due to the transmission differences. The M has a PowrQuad gearbox compared to the DirectDrive in the Rs.”
“The downside is its smaller fuel tank; although it’s not an issue while carting silage, it becomes a problem during springtime power harrowing.”
“It demands refueling more frequently, whereas the Rs can last all night without a refill,” he adds.
Despite this limitation, James anticipates acquiring more M-series tractors in the future, as they are affordable, user-friendly, and excellent for communal yard tasks.
However, achieving optimal value requires careful consideration of specifications, with James expressing frustration over expensive add-ons suggested by the salesman.
“The 6R 175 arrived with auto-steering and section control features, which we didn’t request—it’s primarily a haulage tractor.”
“Without those extras, we could have afforded a 6R 195 instead.”
“Moreover, we were informed we couldn’t have mid-mount valves on the M-series, yet it turns out we could have.”
Improvements in Implements
This year also saw the introduction of a £60,000 Gaspardo maize drill equipped with section control.
While the investment was challenging to justify, it has dramatically improved operational efficiency—capable of maintaining seed placement accuracy at 15 kph, compared to the previous model’s 7 kph maximum.
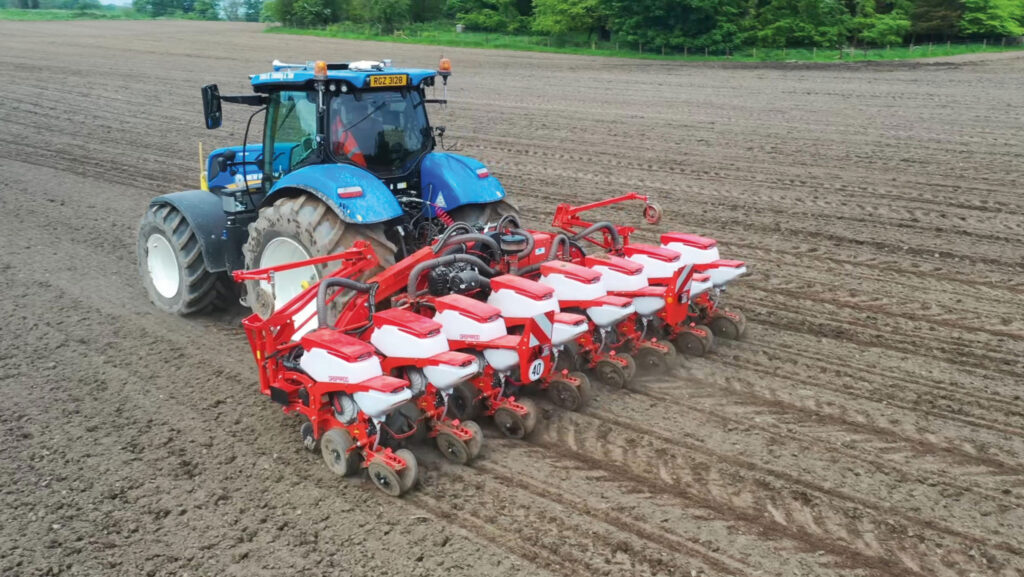
© James Townley
This has significantly reduced the time needed for nearly 300 hectares of late-spring sowing.
Additionally, a Claas Liner 4800 rake was acquired after a last-minute decision to downsize from a 50ft to a 40ft model, which has proven advantageous. The smaller rake allows the Jaguar 970 to operate more effectively by producing a less tangled and compact swath.
The decision to downgrade was influenced by the loss of approximately 400 hectares of grass and maize silage land, plus another 200 hectares of combining work.
“We face significant underbidding from other contractors—even more than our profit margin on jobs—which leaves us puzzled,” James explains.
“Our business primarily relies on farm contracting, making it difficult as we cannot subsidize losses in any way; we need to pass on increasing costs to remain viable.”
“We take pride in providing excellent service and will always welcome clients back, but this market is tough,” he adds.
James believes that the difficulties faced by farmers, contractors, and dealers reflect broader instability in the industry caused by weather unpredictability and financial pressures.
Potential Price Decreases?
“The truth is, we might be in the wrong industry—we should focus on manufacturing machinery rather than purchasing it.”
However, with manufacturers feeling the pinch of declining sales, could equipment prices finally start to drop?
“The stock values of major machinery companies have recently experienced declines, prompting me to wonder how they will navigate these challenges,” he asserts.
This uncertainty has made James hesitant to replace the troublesome T7 in the near future, especially since the dealer has provided exorbitant quotes for a trade-in.
Currently, the depreciation costs amount to £34 per hour, while trading in the T7.
“The T7.245 we demoed was outstanding in comfort, but nearly £1,000 per horsepower is phenomenal, and tractors are becoming overly expensive for what they are.”
“I could invest in a home in Ballygowan for the same price (£180,000), rent it out for three years, and likely sell it at a profit.”
One machine potentially on the chopping block is the four-year-old mounted Amazone UF1602 sprayer, with its replacement probably being another Amazone model due to its proximity to the dealer.
“If I struck it rich in the lottery, I’d opt for a Horsch sprayer—they offer superior boom leveling, which is crucial since our fields are anything but flat.”
“However, the price of a new Amazone has doubled in four years, now reaching £60,000, resulting in annual running costs of £8,000-£10,000; a comparable Horsch model would cost another £20,000, which we simply can’t afford.”
Condensed Growing Season
This year’s weather delays resulted in spring barley being sown during the third week of May, putting planting six weeks behind schedule.
This situation means that combines will be harvesting spring barley well into late September and even October, when morning dews could limit working hours to just a few each day.
So far, crop yields have varied, with winter barley resulting in a loss for the second consecutive year with an average of 4.5t/ha.
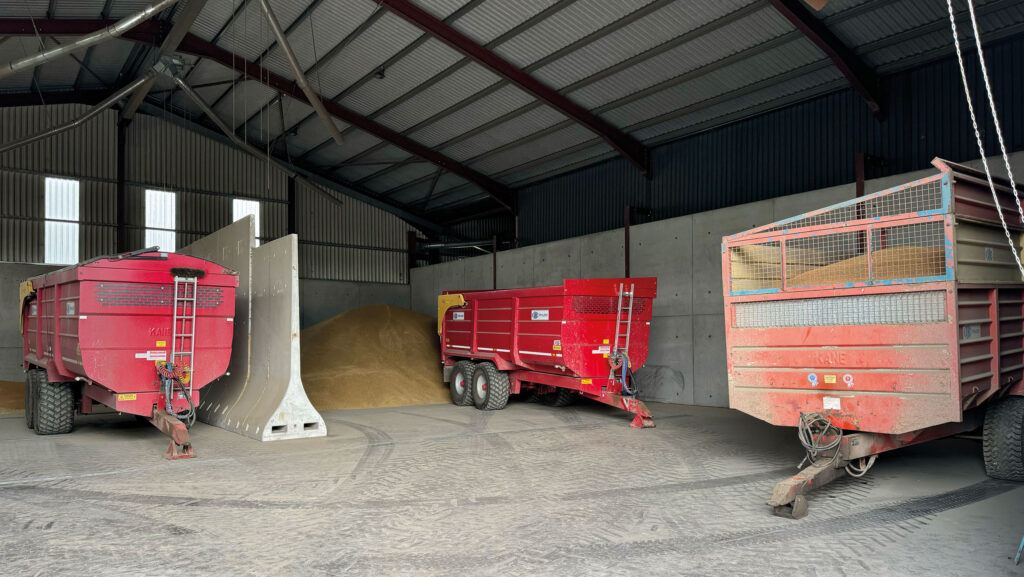
© MAG/Oliver Mark
Fortunately, oilseed rape yields were similar, and its higher value should help offset some losses.
However, due to harvesting delays, it is unlikely that oilseed rape will fit into the rotation for the next year.
“As of late August, we have barely begun harvesting wheat and are still only at the early stages,” James reports.
“Instead, we’ve been busy sorting out field drains with the trencher. But as soon as the weather improves, we might find ourselves overwhelmed with work. Farming is never without its challenges.”
SOURCE

Maria Sanchez completed her Bachelor’s degree in Plant Sciences from the University of California, Davis, in the USA. Her studies focused on plant genetics and biotechnology, with an emphasis on developing disease-resistant crop varieties. Maria has contributed to several research projects aimed at improving crop resilience to climate change and is now pursuing her Master’s degree in Plant Breeding.